“Every piece is created and crafted with the upmost care and consideration. I can’t wait for you to experience the quality and elegance.”
Vanessa Gavin-Headen, СEO Valmasi
Challenge
Valmasi needed to quickly launch production on multiple SKUs with their factory. They were forced with constraints around time, money and expertise.
Creating a robust quality control process required product documentation, inspection requirements and reporting procedures.
The challenge of creating a quality control process left Valmasi with questions like:
- How can we avoid manual data entry and redundant work?
- How do we create product inspections for our factory without hiring a quality engineer?
- How will the factory update us on progress and results of product inspections?
- How do we synthesize inspections reports to understand the level of quality?
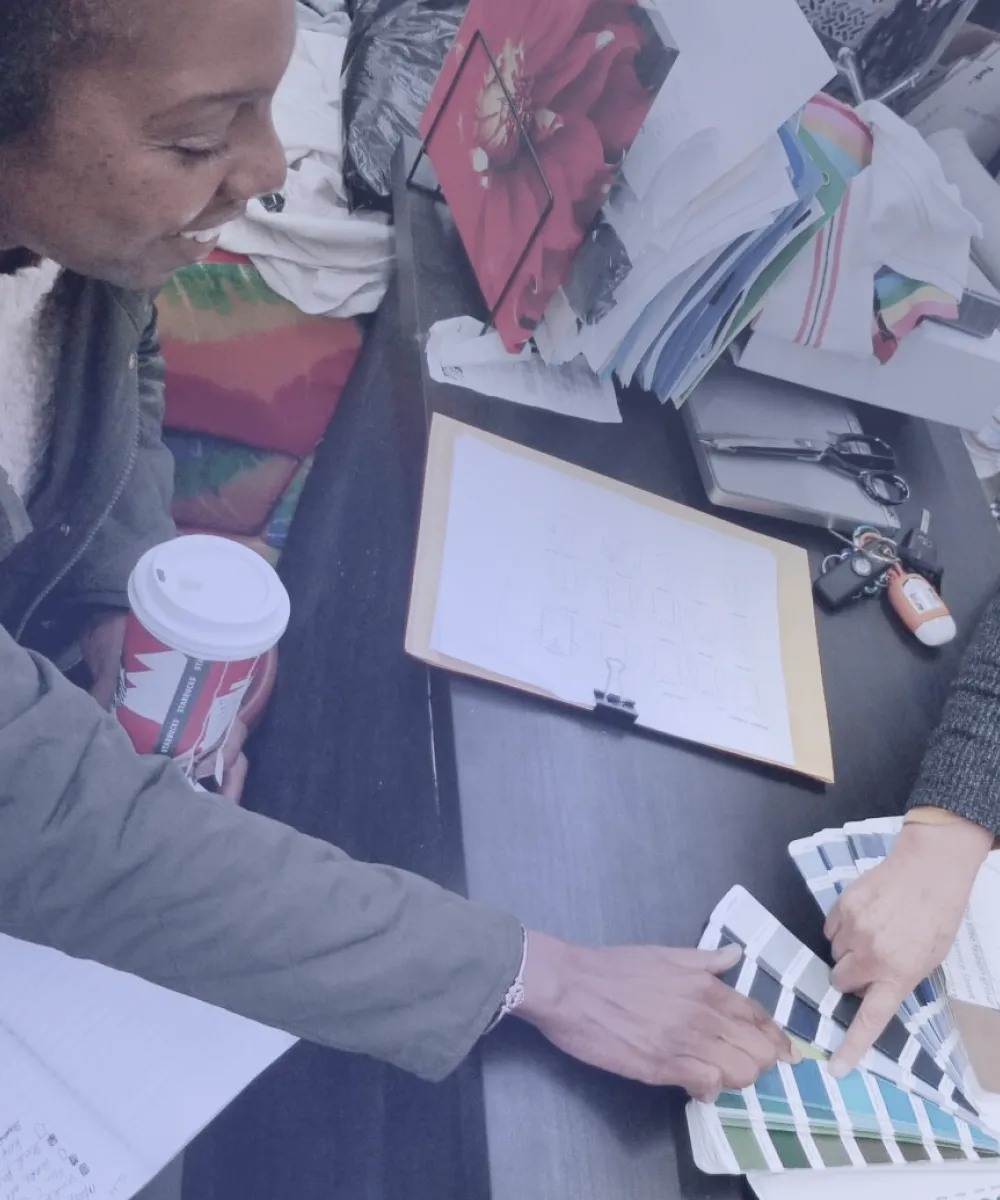
Solution
Vanesssa, CEO of Valmasi, contacted Airbatch looking for a platform solution for quality control.
Airbatch’s self-serve integrations allowed Valmasi to sync to Quickbooks enabling instant onboarding of factories, POs, products and users.
With POs and products now synced into Airbatch, team Valmasi leveraged automations. With a few inputs an AI Agent was deployed to:
- Create inspections for multiple products
- Assign products and inspections to POs
- Design reporting dashboards for inspection results
Within hours Valmasi digitized their supply chain and deployed a quality control platform, ensuring high quality products, happy customers and future profits.
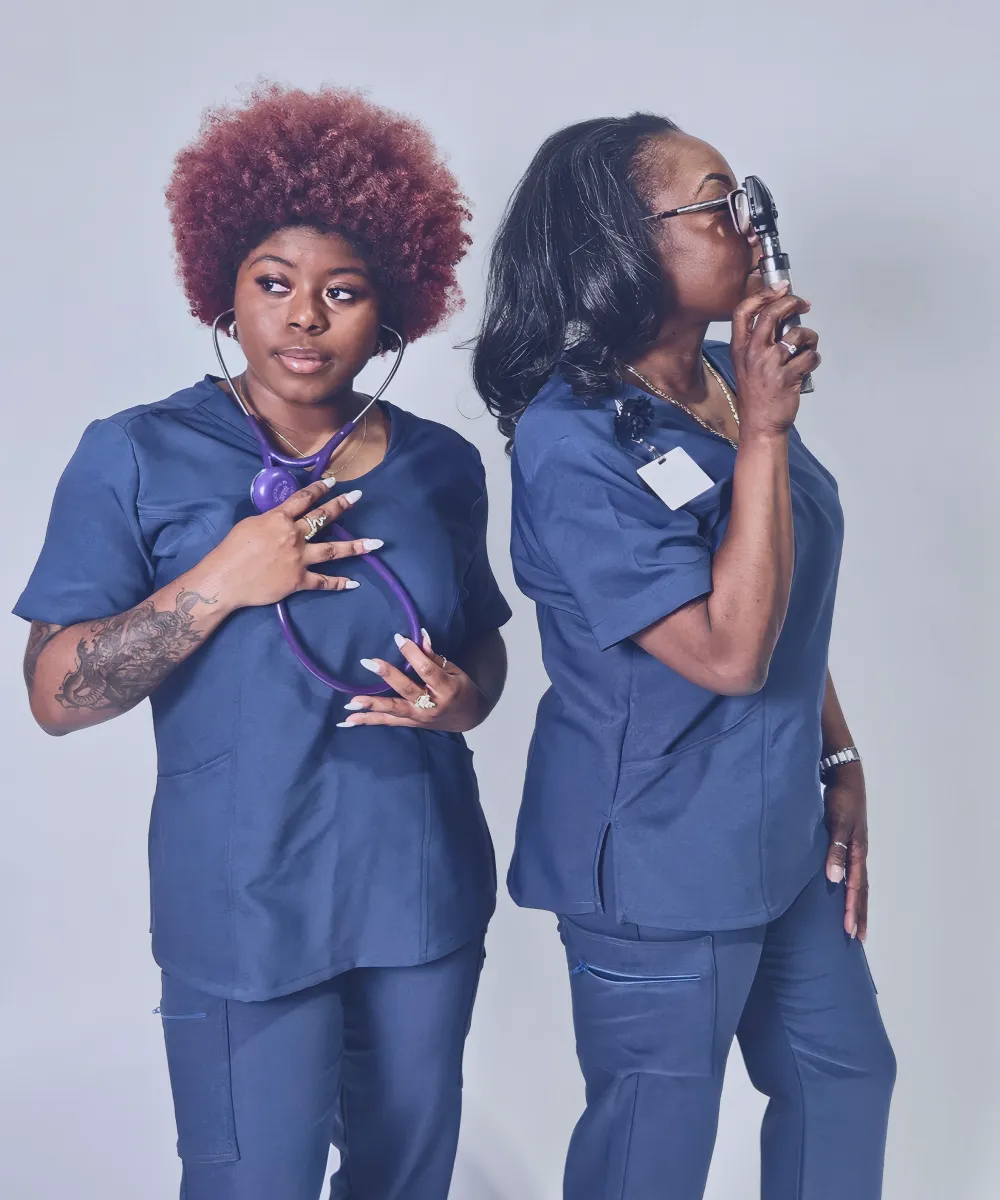
Impact
to deployment
pass rate
expense savings
human labour